MOLY DRY FILM LUBRICANT
AND HOW DOES MOLY LUBRICATE?
A natural lubricant mined principally from ore deposits in the Colorado Rockies, Molybdenum Disulfide (MoS2 or Moly), is one of the best lubricants known to science. Similar in appearance to graphite, Moly is twice as slippery, providing a tough, durable lubricating film. It has a load carrying capacity from 225,000 upwards to 500,000 psi which is beyond the yield strength of most metals. Moving parts are protected by Moly’s magnetic-like attraction to metal. When Moly is applied to metal surfaces and pressure is applied, it fills the pores and “bonds” to the surface, minimizing metal-to-metal contact maintaining an extremely low coefficient of friction. It will build to no more than .0002 of an inch, therefore, tolerances are unaffected. MOLY DRY FILM LUBRICANT is a dispersion of collodial Molybdenum Disulfide and a special binding resin that provides excellent lubricity and wears better than a coating of pure moly. Packaged as a convenient aerosol spray using a hydrocarbon propellant, it forms a tough lubricant film upon curing. Designed for use where a strong but dry lubricating film is required or desired, without the aftereffects of a wet, greasy residual film of conventional lubricants.
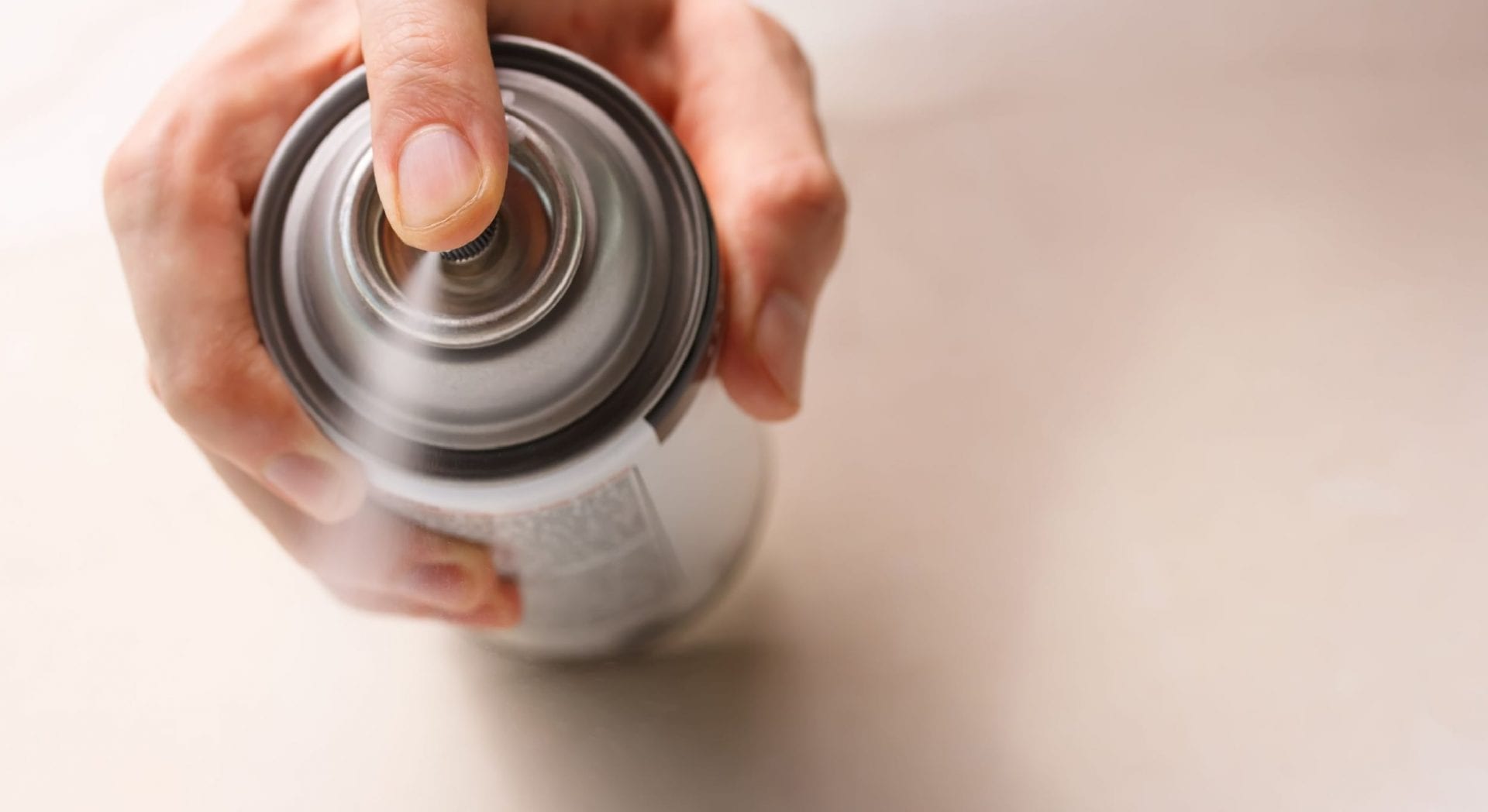
MOLY DRY FILM LUBRICANT HELPS RESIST RUST AND CORROSION
This spray lubricant also provides superior rust and corrosion resistance by its plating action. Since Molybdenum Disulfide is virtually inert, oxidation is kept to a minimum. MOLY DRY FILM can be applied as a strong adhesive film to a wide variety of materials with little or no surface pretreatment required. This includes both ferrous base and alloy metals as well as most other commonly used metals, plastics, woods and glass.
MOLY DRY FILM LUBRICANT WITHSTANDS HIGH TEMPERATURE APPLICATIONS
MOLY DRY FILM LUBRICANT can be used in high temperature applications up to 340°C and in applications where the temperature might go as high as 400°C intermittently. It is a particularly useful lubricant and release compound for applications where extremely high pressures are encountered, including anti-seize and press fit applications.